Technical data and downloads
Find here all the technical information available on the polymers most frequently used in the production of our plastic fasteners and assembly parts.
The data provided are average values which are given for information only and do not claim to be definitive. Our team is at your disposal to help you choose the ideal plastic material for your projects.
How to choose the right plastic for your parts?
Every plastic fastener/protection part has to meet different needs and withstand different stresses. At Bülte, our aim is to help you choose the plastic that best meets your specifications. Thanks to our expertise in plastic injection molding, we can monitor your projects and support you throughout.
There are over 60 different thermoplastic materials. Below are the general characteristics of the most popular thermoplastic polymers we offer in our catalog.
Below, we've put together a reference guide to thermoplastic materials, describing the characteristics, benefits and most common applications of the main plastics we work with: PA 6 and 6.6, glass-filled PA, POM, PP, HDPE, PVDF.
A customised service
Our team is on hand to help you choose the most appropriate plastic for your needs, because the choice of material is crucial to improving the quality and function of the plastic parts selected. For each plastic fastener and assembly part, we can provide you with the technical data sheet relating to the material of the selected product.
Technical information about materials
The technical data given in the following tables is for guidance only and does not claim to be definitive. To establish the suitability of parts and materials offered on our website or in our catalogue, it is suggested that customers make their own tests for which samples are available on request.
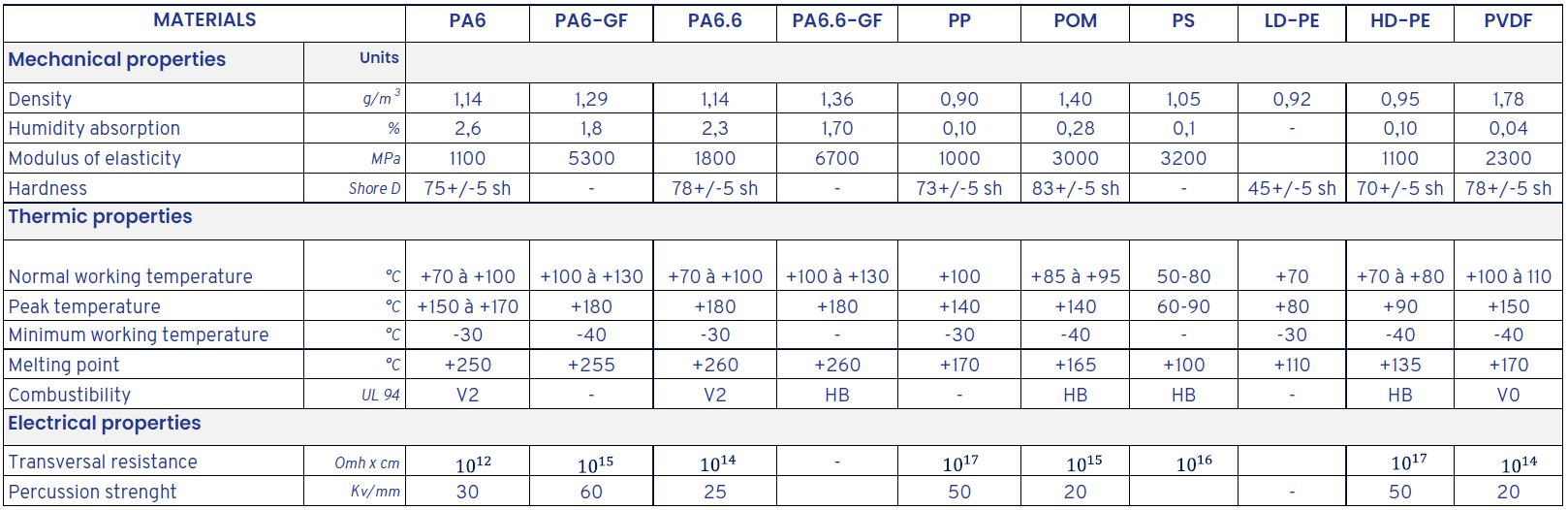
Polyamide 6 and 6.6 - PA
Nylon/PA is a semi-crystalline, low-density thermoplastic with high thermal stability. It is the strongest unreinforced nylon and the most resistant to abrasion and low temperatures. Its good thermal and mechanical properties make polyamide one of the most widely used materials in many industrial sectors, particularly the automotive industry. It is widely used in the manufacture of mechanical parts thanks to its good resistance to basic acids and friction.
Advantages :
- Low coefficient of friction
- Good mechanical, thermal and chemical properties
- Good electrical insulation
- Resistant to oils, greases and solvents
Main applications :
- Automotive
- Domestic appliances
- Electrical engineering
- Mechanical engineering
- Sports and leisure
- Miscellaneous
Glass filled Polyamide 6 and 6.6 - PA-GF
This is an injected material reinforced with glass fibre filler. Glass fibre-reinforced thermoplastic polymers give manufactured parts a remarkable increase in mechanical, thermomechanical and dimensional performance, while retaining the same injection moulding techniques as standard thermoplastics.
Polyamide filled with 30% glass fibre has higher mechanical strength, creep resistance and dimensional stability than non-reinforced polyamide 6.
The properties of PA-GF make this material suitable for applications subject to high static loads over long periods of time, and in high temperature conditions (180° peak). As glass fibres tend to have an abrasive effect, glass-fibre reinforced nylon is less suitable for sliding applications.
Advantages :
- Good mechanical properties
- Impact resistance
- Resistance to thermal ageing
- Enhanced electrical insulation
Main applications :
- Automotive industry
- Electronics
- Mechanical equipment
Polyacetal - POM
Natural POM, also known as Delrin, is an engineering plastic with a wide range of applications compatible with many industries. Its main advantages are excellent wear and abrasion resistance, high rigidity and good chemical resistance. Polyacetal combines a number of physical properties that are not always present in other thermoplastics.
Advantages :
- High mechanical strength
- Creep, impact and wear resistance
- Good sliding properties
- Electrical insulation
Main applications :
- Precision mechanisms
- Automotive components
- Sanitary and medical industries
Polypropylene - PP
PP is a semi-crystalline thermoplastic of the polypropylene type. The main characteristics of natural PP are good corrosion resistance, high rigidity and high heat resistance. It is the ideal material for assembly in acidic environments. We often find this material in the swimming pool sector, in the naval environment such as boat building, as well as in assemblies exposed to salt spray such as beachside installations.
At Bülte, this material is one of the most widely used, particularly in the manufacture of plastic fasteners such as our plastic screws, plastic nuts and plastic washers, but also in the design of plastic bushings and plastic spacers.
Advantages :
- High mechanical properties: high rigidity
- Good resistance to bending, hinge effect
- Thermal and chemical resistance
- Compatibility with food contact
Main applications :
- Shipbuilding
- Medical sector
- Mechanical industry
- Swimming pool and beach installations
High density Polyethylene - HD-PE
PE-HD is a high-molecular-weight polyethylene thermoplastic with better impact resistance and wear resistance than PE-LD (low-density polyethylene). Its main advantages are excellent chemical resistance, high mechanical strength, low moisture absorption and good slip and non-stick properties. Mainly used by Bülte for its range of plastic plugs and caps, this material can also be used for fasteners with plastic bolts (plastic screw-nut-washer assemblies) in PE-HD.
Advantages :
- Food grade
- Chemical stability
- High impact and shock resistance
- Non-stick
- Electrical insulation and UV resistance
Main applications :
- Industrial piping and boiler making
- Industrial machining
- Play areas
- Food containers
Polyvinylidene fluoride - PVDF
PVDF is a semi-crystalline thermoplastic and belongs to the fluoroplastics group. It has the best chemical resistance for the parts offered by Bülte in plastic injection moulding. This material has high mechanical strength, very good chemical resistance and very low moisture absorption. PDVF is ideal for assemblies in highly corrosive environments such as the chemical industry, but also in the energy and hydrocarbons sectors. It can be used in a wide range of temperatures without any loss of mechanical properties: it is a guarantee of safety for the most demanding sectors of industry.
Advantages :
- High chemical resistance to a wide range of oils, greases, alkalis and salt solutions, including at high temperatures
- Mechanical properties, creep resistance
- High wear resistance UL94V-V0 (UV stability - low ageing)
- Excellent thermal stability
- Very low microbiological attachment
Main applications :
- Exterior construction elements: building facades, roofs, etc.
- Electrical cabinets
- Chemical industry
- Medical sector
Personalised information and advice
Most of our plastic fasteners (washers, spacers, nuts, screws, bushings) are made from natural polyamide, the most economical solution. This virgin thermoplastic is ideal for technical parts where the final appearance is not the priority.
Nevertheless, for all your applications requiring a meticulous finish, we can offer high-quality plastic fasteners and assembly parts, in a wide choice of customisable colours.
We can also offer you other plastic and composite materials, if your project so requires, depending on your technical constraints: our experts will study your specifications and we can produce your parts to your drawing.
Material data sheets and a RAL colour chart are available to customers on request: if you would like technical data on the raw materials used in the manufacture of our plastic fasteners and assembly parts, please contact our team. Our experts are on hand to suggest the most appropriate material for your project, taking into account your technical and budgetary constraints. We can also send you free samples for you to test.